Stringent Emissions Standards: Gambling Away Supply Chain Stability
- Kimberly Kraska
- May 15, 2023
- 4 min read
The semiconductor supply chain has experienced major disruptions since 2020 whose effects were projected to last into 2025, and the rapid adoption of electric vehicles in the United States threatens its recovery.
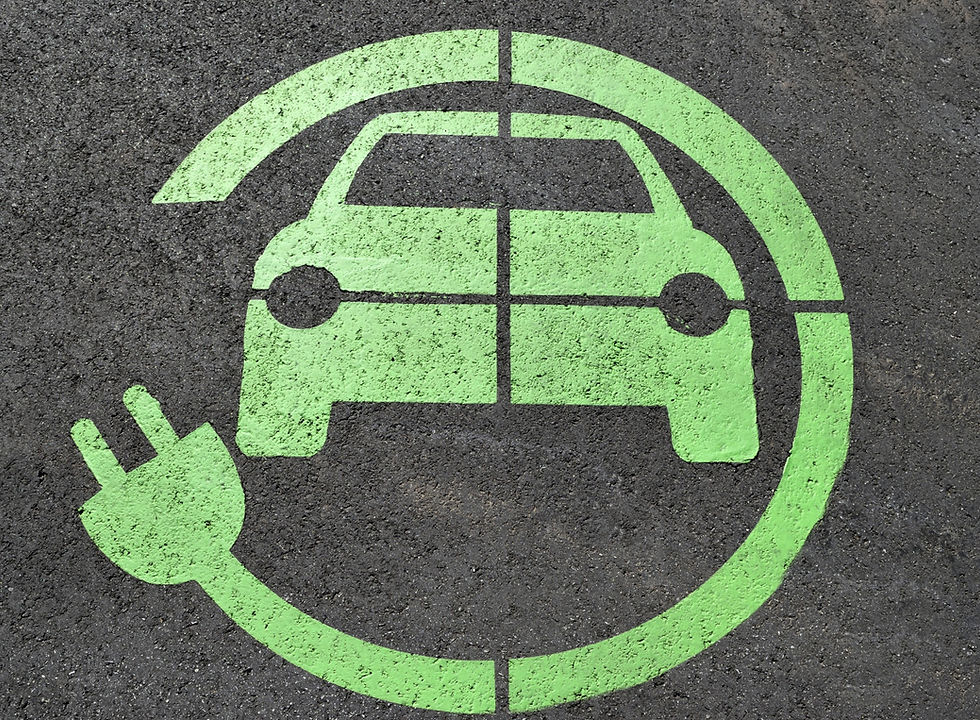
The rollout of the EPA’s most stringent greenhouse gas emission standards (GHG) has the potential to cripple the delicate semiconductor supply chain. The pandemic brought to light the fragility of the international supply chain, with technology sectors disproportionately impacted. The shortage was magnified by restrictions imposed on SMIC, the largest semiconductor chip manufacturer in China, during the US-China trade wars and the lost access to precious metals used to manufacture semiconductors due to the Russia-Ukraine war.
To combat this exposed economic security risk, Congress passed the CHIPS & Science Act in August, 2022. The Semiconductor Industry Association notes that the legislation includes “$52 billion in chip manufacturing incentives and research investments, as well as an investment tax credit for semiconductor manufacturing and semiconductor equipment manufacturing.” The CHIPS Act has been criticized for ineffective allocation of funds by semiconductor experts like Rakesh Kumar, a professor of electrical and computer engineering at University of Illinois. Kumar posits that while bringing manufacturing jobs back to the United States is a politically feasible solution, the reality is that the speed, labor costs, and regulations make even 3 billion dollar grants too low to incentivize semiconductor manufacturing at the necessary scale. Estimates for costs of building a semiconductor fabrication plant are between 4 and 10 billion dollars, which does not account for production costs like labor, maintenance, and materials. Minerals that semiconductors cannot be built without, like gallium and germanium, are referred to as critical minerals. Critical minerals must be processed through a critical minerals-specific refinery, of which the United States has zero. The Biden Administration hopes to remedy this weak link in the supply chain with 156 million in funding allocated to the Department of Energy.
The automotive industry needs chips, and they need a lot of them. The number of semiconductors needed to produce a single vehicle is increasing, as new technology requires higher computing power. Moving to electric vehicles is essential to transition the vehicle fleet from fossil fuels to clean energy. The average internal combustion engine vehicle requires about 600 semiconductors, compared to an average of 1,300 needed to complete a battery-electric vehicle. The quick math on that is that 700 additional semiconductors will need to be produced for each electric car that replaces a traditional vehicle sale. According to Kelley Blue Book, in 2022, “5.8% of the new cars Americans bought were electric, up from 3.2% in 2021. Total EV sales topped 800,000 for the first time”. Many economists have noted that 5% is a significant tipping point for widespread adoption in other countries, and the same is likely to apply in the United States. Mandates like California’s ban on the sale of new gas vehicles beginning in 2035 were expected to be an additional incentive that would spur electric vehicle adoption. However, the EPA’s most recent GHG standards imposed on automakers are now expected to drive the United State’s vehicle fleet to electric.
The EPA projects that proposed standards will ensure electric vehicle sales “account for 67% of new light-duty vehicle sales and 46% of new medium-duty vehicle sales in MY 2032.” That is 10 times the current percentage of total new vehicle sales that are electric. Even California, which has some of the most drastic and progressive net-zero emissions regulations, proposed “35% of new cars, SUVs and small trucks sold to be zero-emissions starting in 2026, increasing to 68% in 2030 and 100% in 2035. In 2022, zero-emissions vehicles have made up about 16% of new cars sold in California.” California developed a comprehensive plan to mitigate the burden on low-income individuals. They have generous grants and tax incentives for individuals in disadvantaged communities or low-income households, whose upper limits range from $7,000 to $9,500. The average ICE vehicle's initial price investment is between $32,000 and $44,000, which is significantly lower than the $65,000 electric vehicle price tag. The aforementioned electric vehicle incentives go a long way in decreasing the initial investment gap, which makes it difficult for low-income households to participate in the clean energy transition. With the automotive fleet rapidly moving to electric, a potential consequence is an increase in the cost of new vehicles, which causes concern that consumers will defer new car purchases. As new vehicles tend to be more energy efficient, the rising cost could actually inhibit the zero carbon goals these strict standards move towards.
The barely recovered and far-from-stable semiconductor market may not be able to keep up with the increased need for semiconductors, and consumers are not ready to suddenly shoulder the burden of a transportation transition which had already reached its tipping point. The EPA’s new emission standards are a bold step to quicken a necessary transition, but there may be unaccounted-for risks associated with a tenfold increase in electric vehicle manufacturing.
Kimberly Kraska is rising third-year CLEG major in the School of Public Affairs. She is a Managing Editor and Director of Administration for the American Agora.
Image Courtesy: Paul Brennan | Public Domain Pictures
Comments